The structures and production processes of natural leather, polyurethane (PU) microfiber synthetic leather and polyvinyl chloride (PVC) synthetic leather were compared, and the material properties were tested, compared and analyzed. The results show that in terms of mechanics, the comprehensive performance of PU microfiber synthetic leather is better than that of genuine leather and PVC synthetic leather; in terms of bending performance, the performance of PU microfiber synthetic leather and PVC synthetic leather is similar, and the bending performance is better than that of genuine leather after aging in wet heat, high temperature, climate alternation, and at low temperature; in terms of wear resistance, the wear and tear resistance of PU microfiber synthetic leather and PVC synthetic leather is better than that of genuine leather; in terms of other material properties, the water vapor permeability of genuine leather, PU microfiber synthetic leather and PVC synthetic leather decreases in turn, and the dimensional stability of PU microfiber synthetic leather and PVC synthetic leather after thermal aging is similar and better than that of genuine leather.
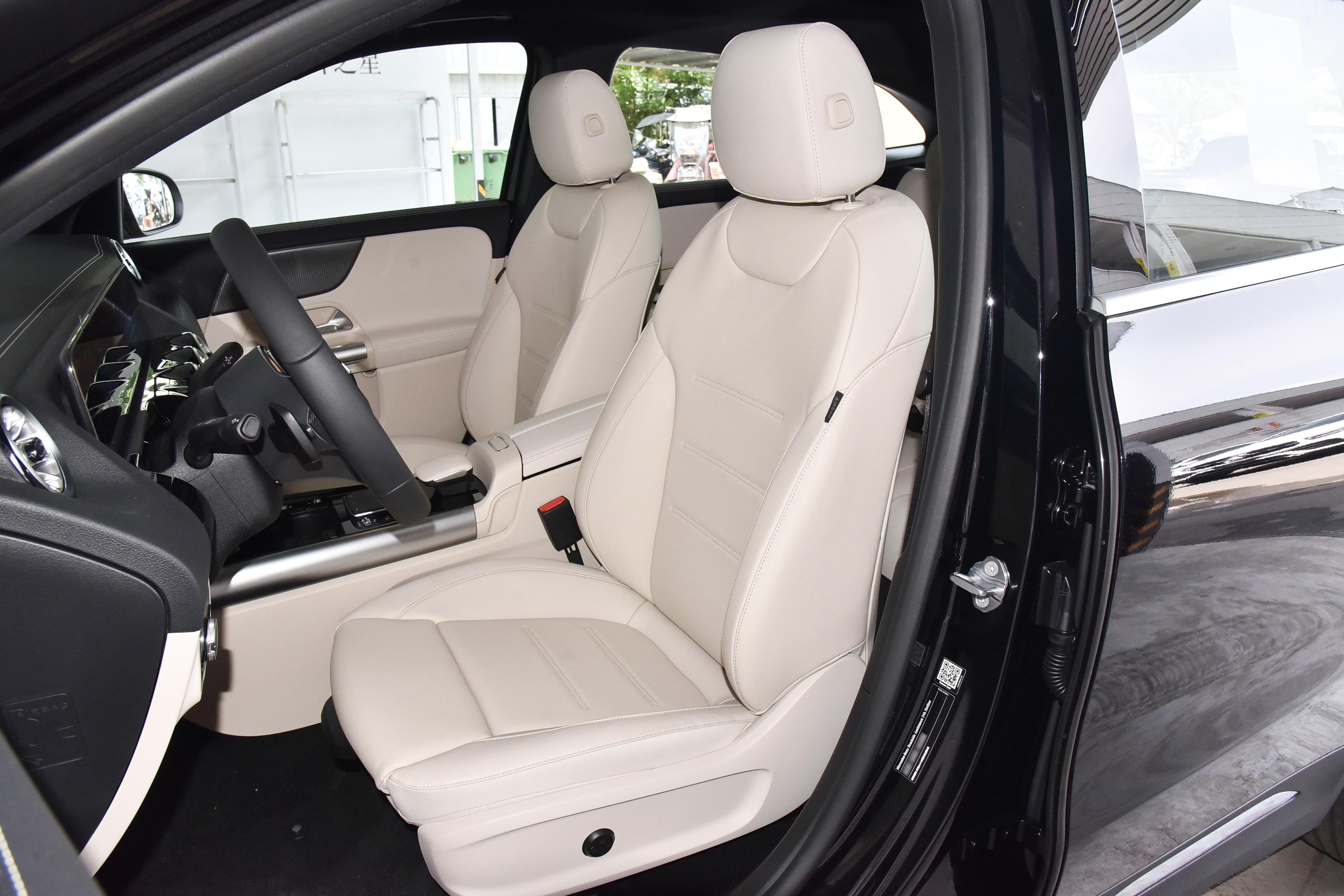
As an important part of car interior, car seat fabrics directly affect the user's driving experience. Natural leather, polyurethane (PU) microfiber synthetic leather (hereinafter referred to as PU microfiber leather) and polyvinyl chloride (PVC) synthetic leather are all commonly used seat fabric materials.
Natural leather has a long history of application in human life. Due to the chemical properties and triple helix structure of collagen itself, it has the advantages of softness, wear resistance, high strength, high moisture absorption and water permeability. Natural leather is mostly used in the seat fabrics of mid-to-high-end models in the automotive industry (mostly cowhide), which can combine luxury and comfort.
With the development of human society, the supply of natural leather is difficult to meet people's growing demand. People began to use chemical raw materials and methods to make substitutes for natural leather, that is, artificial synthetic leather. The advent of PVC synthetic leather can be traced back to the 20th In the 1930s, it was the first generation of artificial leather products. Its material characteristics are high strength, wear resistance, folding resistance, acid and alkali resistance, etc., and it is low cost and easy to process. PU microfiber leather was successfully developed in the 1970s. After the progress and improvement of modern technology applications, as a new type of artificial synthetic leather material, it has been widely used in high-end clothing, furniture, balls, car interiors and other fields. The material characteristics of PU microfiber leather are that it truly simulates the internal structure and texture quality of natural leather, and has better durability than genuine leather, more material cost advantages and environmental friendliness.
Experimental part
PVC synthetic leather
The material structure of PVC synthetic leather is mainly divided into It is the surface coating, PVC dense layer, PVC foam layer, PVC adhesive layer and polyester base fabric (see Figure 1). In the release paper method (transfer coating method), the PVC slurry is first scraped for the first time to form a PVC dense layer (surface layer) on the release paper, and enters the first oven for gel plasticization and cooling; secondly, after the second scraping, a PVC foam layer is formed on the basis of the PVC dense layer, and then plasticized and cooled in the second oven; thirdly, after the third scraping, a PVC adhesive layer (bottom layer) is formed, and it is bonded with the base fabric, and enters the third oven for plasticization and foaming; finally, it is peeled off from the release paper after cooling and forming (see Figure 2).
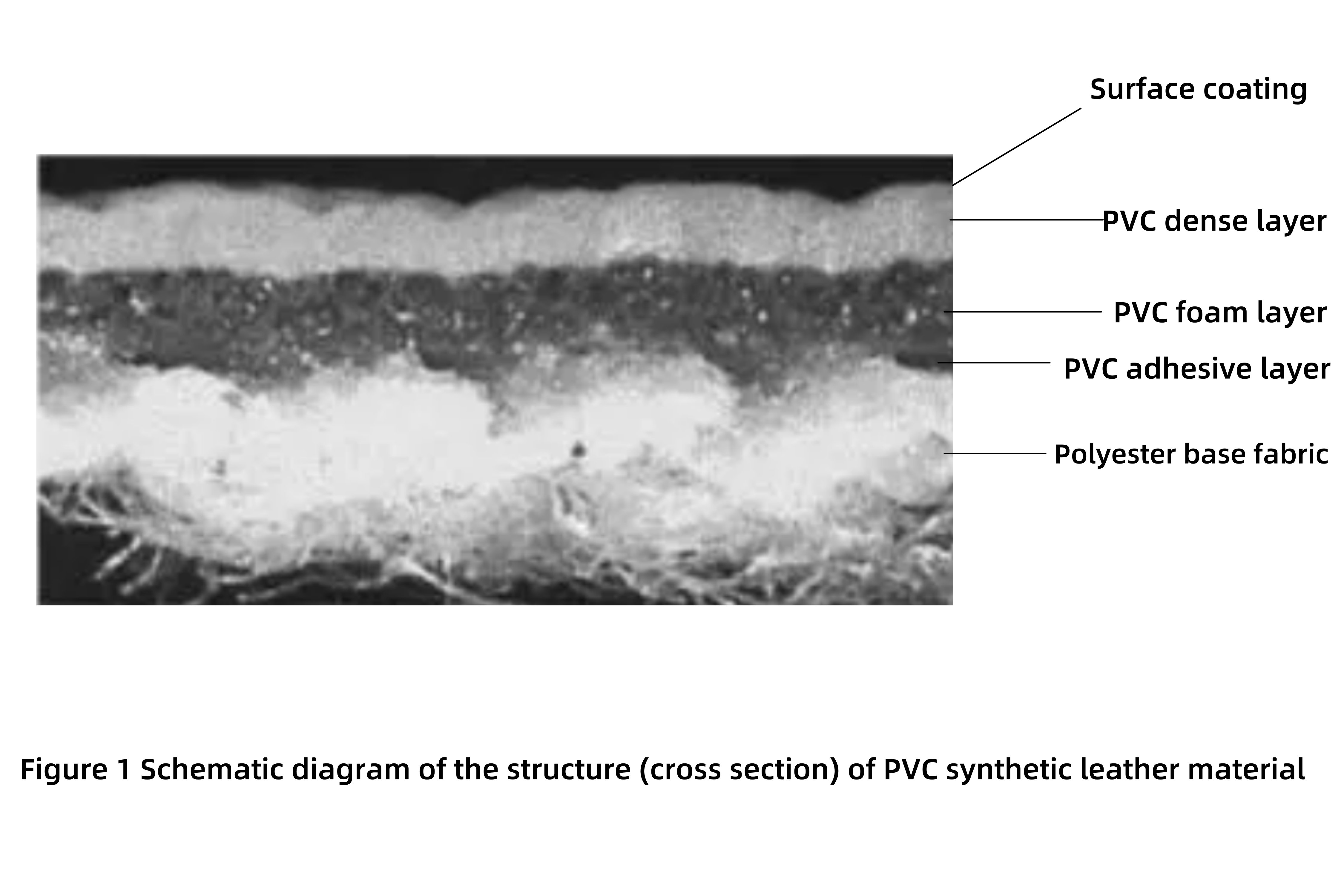
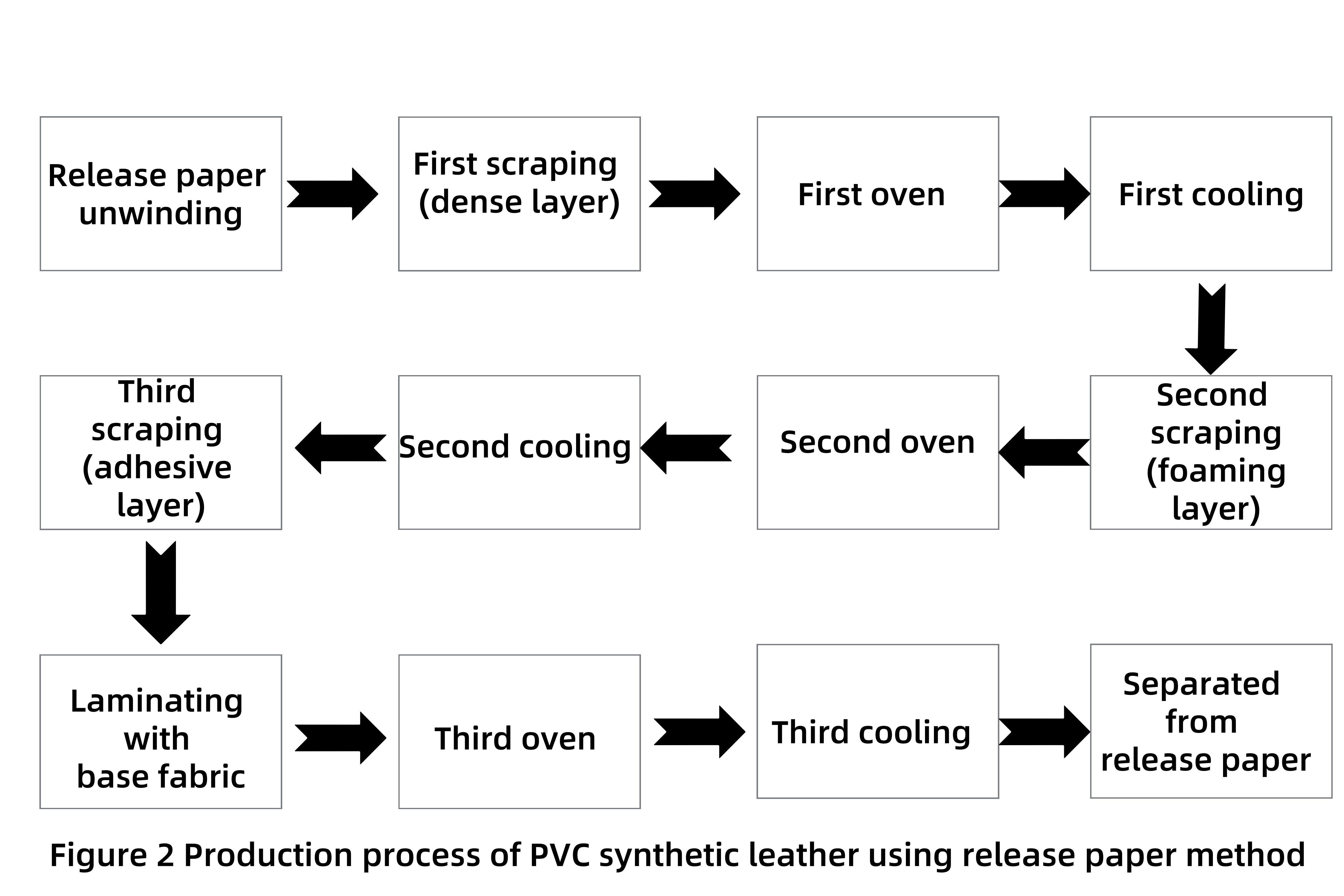
Natural leather and PU microfiber leather
The material structure of natural leather includes grain layer, fiber structure and surface coating (see Figure 3(a)). The production process from raw leather to synthetic leather is generally divided into three stages: preparation, tanning and finishing (see Figure 4). The original intention of the design of PU microfiber leather is to truly simulate natural leather in terms of material structure and appearance texture. The material structure of PU microfiber leather mainly includes PU layer, base part and surface coating (see Figure 3(b)). Among them, the base part uses bundled microfibers with similar structure and performance to bundled collagen fibers in natural leather. Through special process treatment, a high-density non-woven fabric with a three-dimensional network structure is synthesized, combined with PU filling material with an open microporous structure (see Figure 5).
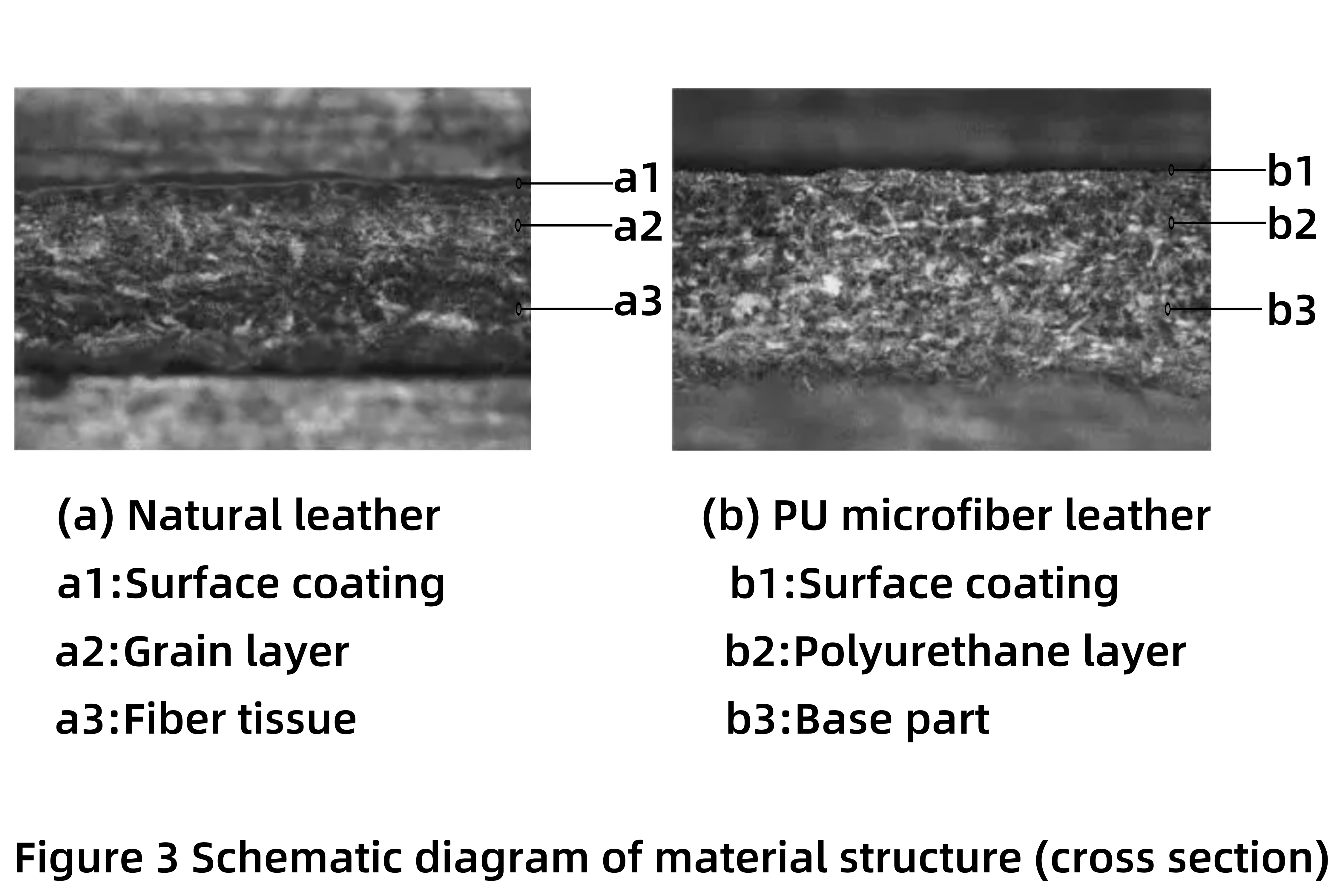
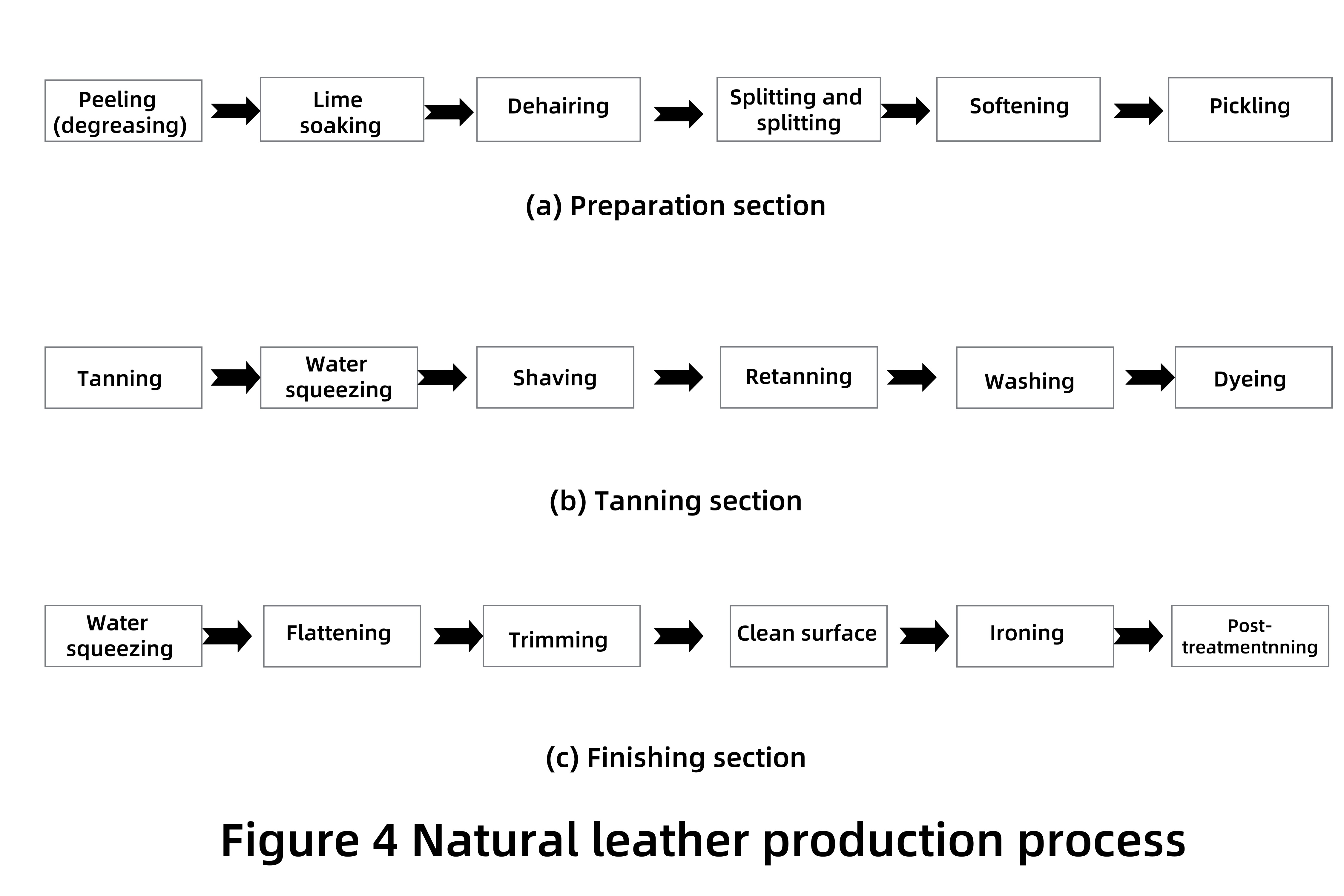
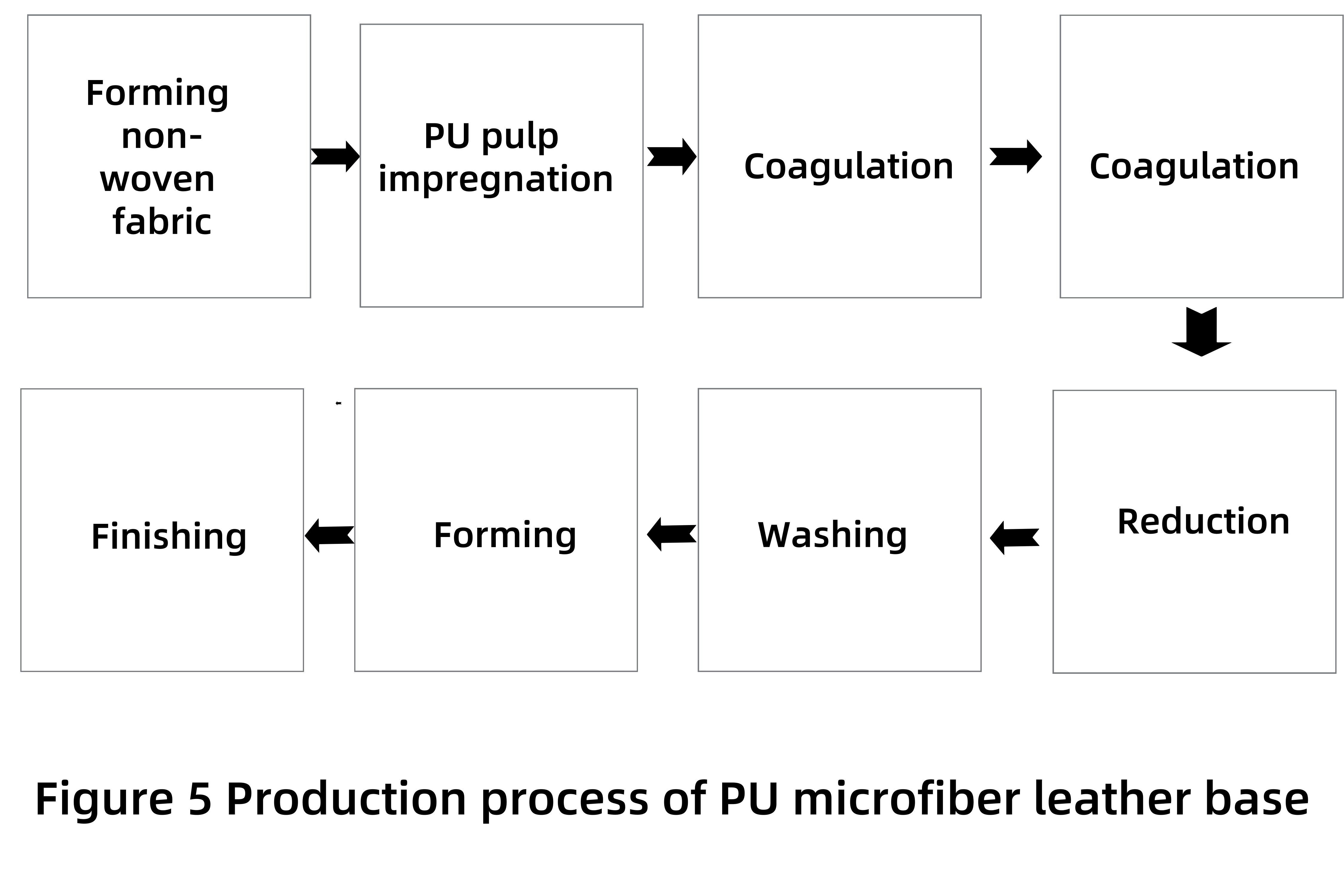
Sample preparation
The samples come from the mainstream automotive seat fabric suppliers in the domestic market. Two samples of each material, genuine leather, PU microfiber leather and PVC synthetic leather, are prepared from 6 different suppliers. The samples are named genuine leather 1# and 2#, PU microfiber leather 1# and 2#, PVC synthetic leather 1# and 2#. The color of the samples is black.
Testing and characterization
Combined with the requirements of vehicle applications for materials, the above samples are compared in terms of mechanical properties, folding resistance, wear resistance and other material properties. The specific test items and methods are shown in Table 1.
Table 1 Specific test items and methods for material performance testing
No. | Performance classification | Test items | Equipment name | Test method |
1 | Main mechanical properties | Tensile strength/elongation at break | Zwick tensile testing machine | DIN EN ISO 13934-1 |
Tear force | Zwick tensile testing machine | DIN EN ISO 3377-1 | ||
Static elongation/permanent deformation | Suspension bracket, weights | PV 3909(50 N/30 min) | ||
2 | Folding resistance | Folding test | Leather bending tester | DIN EN ISO 5402-1 |
3 | Abrasion resistance | Color fastness to friction | Leather friction tester | DIN EN ISO 11640 |
Ball plate abrasion | Martindale abrasion tester | VDA 230-211 | ||
4 | Other material properties | Water permeability | Leather moisture tester | DIN EN ISO 14268 |
Horizontal flame retardancy | Horizontal flame retardant measuring equipment | TL. 1010 | ||
Dimensional stability (shrinkage rate) | High temperature oven, climate change chamber, ruler | - | ||
Odor emission | High temperature oven, odor collection device | VW50180 |
Analysis and discussion
Mechanical properties
Table 2 shows the mechanical properties test data of genuine leather, PU microfiber leather and PVC synthetic leather, where L represents the material warp direction and T represents the material weft direction. It can be seen from Table 2 that in terms of tensile strength and elongation at break, the tensile strength of natural leather in both the warp and weft directions is higher than that of PU microfiber leather, showing better strength, while the elongation at break of PU microfiber leather is greater and the toughness is better; while the tensile strength and elongation at break of PVC synthetic leather are both lower than those of the other two materials. In terms of static elongation and permanent deformation, the tensile strength of natural leather is higher than that of PU microfiber leather, showing better strength, while the elongation at break of PU microfiber leather is greater and the toughness is better. In terms of deformation, the permanent deformation of PU microfiber leather is the smallest in both the warp and weft directions (the average permanent deformation in the warp direction is 0.5%, and the average permanent deformation in the weft direction is 2.75%), indicating that the material has the best recovery performance after being stretched, which is better than genuine leather and PVC synthetic leather. Static elongation refers to the degree of elongation deformation of the material under stress conditions during the assembly of the seat cover. There is no clear requirement in the standard and it is only used as a reference value. In terms of tearing force, the values of the three material samples are similar and can meet the standard requirements.
Table 2 Mechanical properties test results of genuine leather, PU microfiber leather and PVC synthetic leather
Sample | Tensile strength/MPa | Elongation at break/% | Static elongation/% | Permanent deformation/% | Tear force/N | |||||
L | T | L | T | L | T | L | T | L | T | |
Genuine leather 1# | 17.7 | 16.6 | 54.4 | 50.7 | 19.0 | 11.3 | 5.3 | 3.0 | 50 | 52.4 |
Genuine leather 2# | 15.5 | 15.0 | 58.4 | 58.9 | 19.2 | 12.7 | 4.2 | 3.0 | 33.7 | 34.1 |
Genuine leather standard | ≥9.3 | ≥9.3 | ≥30.0 | ≥40.0 | ≤3.0 | ≤4.0 | ≥25.0 | ≥25.0 | ||
PU microfiber leather 1# | 15.0 | 13.0 | 81.4 | 120.0 | 6.3 | 21.0 | 0.5 | 2.5 | 49.7 | 47.6 |
PU microfiber leather 2# | 12.9 | 11.4 | 61.7 | 111.5 | 7.5 | 22.5 | 0.5 | 3.0 | 67.8 | 66.4 |
PU Microfiber leather standard | ≥9.3 | ≥9.3 | ≥30.0 | ≥40.0 | ≤3.0 | ≤4.0 | ≥40.0 | ≥40.0 | ||
PVC synthetic leather I# | 7.4 | 5.9 | 120.0 | 130.5 | 16.8 | 38.3 | 1.2 | 3.3 | 62.5 | 35.3 |
PVC synthetic leather 2# | 7.9 | 5.7 | 122.4 | 129.5 | 22.5 | 52.0 | 2.0 | 5.0 | 41.7 | 33.2 |
PVC synthetic leather standard | ≥3.6 | ≥3.6 | ≤3.0 | ≤6.0 | ≥30.0 | ≥25.0 |
In general, the PU microfiber leather samples have good tensile strength, elongation at break, permanent deformation and tearing force, and the comprehensive mechanical properties are better than those of genuine leather and PVC synthetic leather samples.
Folding resistance
The states of the folding resistance test samples are specifically divided into 6 types, namely initial state (unaged state), damp heat aging state, low temperature state (-10℃), xenon light aging state (PV1303/3P), high temperature aging state (100℃/168h) and climate alternation aging state (PV12 00/20P). The folding method is to use a leather bending instrument to fix the two ends of the rectangular sample in the length direction on the upper and lower clamps of the instrument, so that the sample is 90°, and repeatedly bends at a certain speed and angle. The folding performance test results of genuine leather, PU microfiber leather and PVC synthetic leather are shown in Table 3. It can be seen from Table 3 that the genuine leather, PU microfiber leather and PVC synthetic leather samples are all folded after 100,000 times in the initial state and 10,000 times in the aging state under xenon light. It can maintain a good state without cracks or stress whitening. In other different aging states, namely, the wet heat aging state, high temperature aging state, and climate alternation aging state of PU microfiber leather and PVC synthetic leather, the samples can withstand 30,000 bending tests. After 7,500 to 8,500 bending tests, cracks or stress whitening began to appear in the wet heat aging state and high temperature aging state samples of genuine leather, and the severity of wet heat aging (168h/70℃/75%) is lower than that of PU microfiber leather. Fiber leather and PVC synthetic leather (240h/90℃/95%). Similarly, after 14,000~15,000 bending tests, cracks or stress whitening appear in the state of leather after climate alternation aging. This is because the bending resistance of leather mainly depends on the natural grain layer and fiber structure of the original leather, and its performance is not as good as that of chemical synthetic materials. Correspondingly, the material standard requirements for leather are also lower. This shows that the leather material is more "delicate" and users need to be more cautious or pay attention to maintenance during use.
Table 3 Folding performance test results of genuine leather, PU microfiber leather and PVC synthetic leather
Sample | Initial state | Wet heat aging state | Low temperature state | Xenon light aging state | High temperature aging state | Climate alternation aging state |
Genuine leather 1# | 100,000 times, no cracks or stress whitening | 168 h/70 ℃/75% 8 000 times, cracks began to appear, stress whitening | 32 000 times, cracks began to appear, no stress whitening | 10 000 times, no cracks or stress whitening | 7500 times, cracks began to appear, no stress whitening | 15 000 times, cracks began to appear, no stress whitening |
Genuine leather 2# | 100,000 times, no cracks or stress whitening | 168 h/70 ℃/75% 8 500 times, cracks began to appear, stress whitening | 32 000 times, cracks began to appear, no stress whitening | 10 000 times, no cracks or stress whitening | 8000 times, cracks began to appear, no stress whitening | 4000 times, cracks began to appear, no stress whitening |
PU microfiber leather 1# | 100,000 times, no cracks or stress whitening | 240 h/90 ℃/95% 30 000 times, no cracks or stress whitening | 35 000 times, no cracks or stress whitening | 10 000 times, no cracks or stress whitening | 30 000 times, no cracks or stress whitening | 30 000 times, no cracks or stress whitening |
PU microfiber leather 2# | 100,000 times, no cracks or stress whitening | 240 h/90 ℃/95% 30 000 times, no cracks or stress whitening | 35 000 times, no cracks or stress whitening | 10 000 times, no cracks or stress whitening | 30 000 times, no cracks or stress whitening | 30 000 times, no cracks or stress whitening |
PVC synthetic leather 1# | 100,000 times, no cracks or stress whitening | 240 h/90 ℃/95% 30 000 times, no cracks or stress whitening | 35 000 times, no cracks or stress whitening | 10 000 times, no cracks or stress whitening | 30 000 times, no cracks or stress whitening | 30 000 times, no cracks or stress whitening |
PVC synthetic leather 2# | 100,000 times, no cracks or stress whitening | 240 h/90 ℃/95% 30 000 times, no cracks or stress whitening | 35 000 times, no cracks or stress whitening | 10 000 times, no cracks or stress whitening | 30 000 times, no cracks or stress whitening | 30 000 times, no cracks or stress whitening |
Genuine leather standard requirements | 100,000 times, no cracks or stress whitening | 168 h/70 ℃/75% 5 000 times, no cracks or stress whitening | 30 000 times, no cracks or stress whitening | 10 000 times, no cracks or stress whitening | No requirements | No requirement |
PU microfiber leather standard requirements | 100,000 times, no cracks or stress whitening | 240 h/90 ℃/95% 30 000 times, no cracks or stress whitening | 30 000 times, no cracks or stress whitening | 10 000 times, no cracks or stress whitening | 30 000 times, no cracks or stress whitening | 30 000 times, no cracks or stress whitening |
In general, the folding performance of leather, PU microfiber leather and PVC synthetic leather samples is good in the initial state and xenon light aging state. In the wet heat aging state, low temperature state, high temperature aging state and climate change aging state, the folding performance of PU microfiber leather and PVC synthetic leather is similar, which is better than that of leather.
Abrasion resistance
The abrasion resistance test includes friction color fastness test and ball plate abrasion test. The wear resistance test results of leather, PU microfiber leather and PVC synthetic leather are shown in Table 4. The friction color fastness test results show that the leather, PU microfiber leather and PVC synthetic leather samples are in the initial state, deionized water soaked state, alkaline sweat soaked state and When soaked in 96% ethanol, the color fastness after friction can be maintained above 4.0, and the color state of the sample is stable and will not fade due to surface friction. The results of the ball plate abrasion test show that after 1800-1900 times of wear, the leather sample has about 10 damaged holes, which is significantly different from the wear resistance of PU microfiber leather and PVC synthetic leather samples (both have no damaged holes after 19,000 times of wear). The reason for the damaged holes is that the grain layer of the leather is damaged after wear, and its wear resistance is quite different from that of chemical synthetic materials. Therefore, the weak wear resistance of leather also requires users to pay attention to maintenance during use.
Table 4 Test results of wear resistance of genuine leather, PU microfiber leather and PVC synthetic leather | |||||
Samples | Color fastness to friction | Ball plate wear | |||
Initial state | Deionized water soaked state | Alkaline sweat soaked state | 96% ethanol soaked state | Initial state | |
(2000 times friction) | (500 times friction) | (100 times friction) | (5 times friction) | ||
Genuine leather 1# | 5.0 | 4.5 | 5.0 | 5.0 | About 1900 times 11 damaged holes |
Genuine leather 2# | 5.0 | 5.0 | 5.0 | 4.5 | About 1800 times 9 damaged holes |
PU microfiber leather 1# | 5.0 | 5.0 | 5.0 | 4.5 | 19 000 times No surface damaged holes |
PU microfiber leather 2# | 5.0 | 5.0 | 5.0 | 4.5 | 19 000 times without surface damage holes |
PVC synthetic leather 1# | 5.0 | 4.5 | 5.0 | 5.0 | 19 000 times without surface damage holes |
PVC synthetic leather 2# | 5.0 | 5.0 | 5.0 | 4.5 | 19 000 times without surface damage holes |
Genuine leather standard requirements | ≥4.5 | ≥4.5 | ≥4.5 | ≥4.0 | 1500 times of wear and tear No more than 4 damage holes |
Synthetic leather standard requirements | ≥4.5 | ≥4.5 | ≥4.5 | ≥4.0 | 19000 times of wear and tear No more than 4 damage holes |
In general, genuine leather, PU microfiber leather and PVC synthetic leather samples all have good friction color fastness, and PU microfiber leather and PVC synthetic leather have better wear and tear resistance than genuine leather, which can effectively prevent wear and tear.
Other material properties
The test results of water permeability, horizontal flame retardancy, dimensional shrinkage and odor level of genuine leather, PU microfiber leather and PVC synthetic leather samples are shown in Table 5.
Table 5 Test results of other material properties of genuine leather, PU microfiber leather and PVC synthetic leather | ||||
Sample | Water permeability/(mg/10cm²·24h) | Horizontal flame retardancy/(mm/min) | Dimensional shrinkage/%(120℃/168 h) | Odor level |
Genuine leather 1# | 3.0 | Non-flammable | 3.4 | 3.7 |
Genuine leather 2# | 3.1 | Non-flammable | 2.6 | 3.7 |
PU microfiber leather 1# | 1.5 | Non-flammable | 0.3 | 3.7 |
PU microfiber leather 2# | 1.7 | Non-flammable | 0.5 | 3.7 |
PVC synthetic leather 1# | Not tested | Non-flammable | 0.2 | 3.7 |
PVC synthetic leather 2# | Not tested | Non-flammable | 0.4 | 3.7 |
Genuine leather standard requirements | ≥1.0 | ≤100 | ≤5 | ≤3.7 (deviation acceptable) |
PU microfiber leather standard requirements | No requirement | ≤100 | ≤2 | ≤3.7 (deviation acceptable) |
PVC synthetic leather standard requirements | No requirement | ≤100 | No requirement | ≤3.7 (deviation acceptable) |
The main differences in the test data are water permeability and dimensional shrinkage. The water permeability of leather is nearly twice that of PU microfiber leather, while PVC synthetic leather has almost no water permeability. This is because the three-dimensional network skeleton (non-woven fabric) in PU microfiber leather is similar to the natural bundle collagen fiber structure of leather, both of which have microporous structures, making both have certain water permeability. Furthermore, the cross-sectional area of collagen fibers in leather is larger and more evenly distributed, and the proportion of microporous space is greater than that of PU microfiber leather, so leather has the best water permeability. In terms of dimensional shrinkage, after heat aging (120℃/1 The shrinkage rates of PU microfiber leather and PVC synthetic leather samples after heat aging (68h) are similar and significantly lower than that of genuine leather, and their dimensional stability is better than that of genuine leather. In addition, the test results of horizontal flame retardancy and odor level show that genuine leather, PU microfiber leather and PVC synthetic leather samples can reach similar levels, and can meet the material standard requirements in terms of flame retardancy and odor performance.
In general, the water vapor permeability of genuine leather, PU microfiber leather and PVC synthetic leather samples decreases in turn. The shrinkage rates (dimensional stability) of PU microfiber leather and PVC synthetic leather after heat aging are similar and better than genuine leather, and the horizontal flame retardancy is better than that of genuine leather. The ignition and odor properties are similar.
Conclusion
The cross-sectional structure of PU microfiber leather is similar to that of natural leather. The PU layer and the base part of PU microfiber leather correspond to the grain layer and the fiber tissue part of the latter. The material structures of the dense layer, foaming layer, adhesive layer and base fabric of PU microfiber leather and PVC synthetic leather are obviously different.
The material advantage of natural leather is that it has good mechanical properties (tensile strength ≥15MPa, elongation at break>50%) and water permeability. The material advantage of PVC synthetic leather is wear resistance (no damage after 19,000 times of ball board wear), and it is resistant to different environmental conditions. The parts have good durability (including resistance to moisture and heat, high temperature, low temperature, and alternating climates) and good dimensional stability (dimensional shrinkage <5% under 120℃/168h). PU microfiber leather has the material advantages of both genuine leather and PVC synthetic leather. The test results of mechanical properties, folding performance, wear resistance, horizontal flame retardancy, dimensional stability, odor level, etc. can reach the best level of natural genuine leather and PVC synthetic leather, and at the same time have certain water permeability. Therefore, PU microfiber leather can better meet the application requirements of car seats and has broad application prospects.
Post time: Nov-19-2024