Product Description
Glitter leather
Glitter powder is stuck on PU leather or PVC to make the leather a special shiny leather. This is collectively called "glitter leather" in the leather industry. The scope of application is getting wider and wider, and it has developed from shoe materials to handicrafts, accessories, decoration materials, etc.
Production Process
Glitter powder is made of polyester (PET) film that is first electroplated into silvery white, then painted and stamped. The surface forms a bright and eye-catching effect. Its shape has four corners and hexagons, and the specifications are determined by the side length. , such as the side lengths of the four corners are generally 0.1mm, 0.2mm and 0.3 mm, etc.
Due to its coarse particles, if you use the general scraping method of polyurethane artificial leather, it is easy to scratch the release paper on the one hand. On the other hand, due to the limitation of sizing amount, it is difficult for the glitter powder to fully cover the color of the polyurethane base, resulting in uneven color. At this stage, manufacturers generally use the spraying method of production: first apply a layer of polyurethane adhesive on the polyurethane wet-process artificial leather, then spray glitter powder and flatten it appropriately to improve its fastness, and then apply it at 140~ Dry at 160℃ and mature for 12~24 hours. After the adhesive is fully cured, clean up the excess glitter powder with a bristle broom. The glitter leather produced by this method has a strong three-dimensional effect, bright colors, and reflects different lusters from different angles, but has poor wear resistance.
Surface glue spraying method
On the glitter leather produced by the spraying method, first use a broom to sweep away the excess glitter powder with low adhesion, and then use a spray gun to spray low viscosity, high solid content, and high gloss on the surface. Polyurethane transparent resin is then dried at 80~120℃, so that the PU resin forms a thin protective layer on the surface of the glitter powder, and improves the adhesion between the glitter powder, greatly improving its It has high abrasion resistance and can maintain its unique multi-angle reflection effect. In order to reduce the impact of pores caused by the solvent drying on the transparency, the method of spraying and drying in stages can be adopted to improve the transparency.
Release paper coating method
The release paper coating method is to add a layer of dry-process transparent resin to the surface of glitter leather, and its production method refers to dry-process polyurethane. Use the glitter leather produced by the spraying method as the base material to laminate on the release paper. The specific process is as follows: mirror release paper - coated with transparent polyurethane resin - 130 ~ 150℃ x 1.5 min drying - coated and double coated Components: polyurethane adhesive - Micro-bake at 40~50℃ - Composite glitter leather - Mature and solidify for 12~24 hours - Separate the glitter leather from the release paper and roll it.
The surface of the coated glitter leather forms a thin, mirror-like transparent protective layer, which enables the leather to achieve the same wear resistance as polyurethane artificial leather, greatly improve its bending resistance, and maintain its softness. It is highly durable and has a crystal effect on its surface. It can be used in the production of sports shoes, belt bags, etc. that require high wear resistance.
compound method
The compounding method is to compound a layer of transparent film on the surface of glittering leather. The process is as follows: first, use a hair broom to sweep away the excess glittering powder with poor adhesion on the glittering leather produced by the spraying method. Clean, then spray an appropriate amount of highly transparent hot-melt polyurethane adhesive, and use a mirror wheel to compound it with a TPU transparent film with a thickness of 0.07~0.10mm at 150~160℃ to form a layer on the surface of the glitter leather. protective layer to improve its wear resistance.
The key to the composite method is the selection of hot-melt polyurethane adhesive, TPU transparent film and composite conditions. On the one hand, hot melt polyurethane adhesives should have high transparency and good resistance to yellowing. On the other hand, the melting point should be between 150 and 160°C. The thickness and hardness of the TPU transparent film should be moderate. The TPU transparent film is too thick, which affects the feel and transparency. , too thin affects the surface flatness, the general thickness is 0.07~0.10 mm; when the hardness is too high, the composite leather will feel too hard, and if it is too low, it will be difficult to operate. Generally, the Shore A hardness is 50~80; mirror surface must be used when compounding The wheel is compounded with 30kg pressure to ensure its fastness.
Process comparison
The above three processing methods each have their own advantages and disadvantages. The surface of the spray-glued leather still maintains its concave and convex feel, and the wear resistance is significantly improved, but the bending resistance is not improved much. The coating method will make the surface smooth and greatly maintain its softness. It has excellent wear resistance but is prone to wrinkles when bent. The composite method also makes the surface smooth and has excellent wear resistance and bending resistance. However, because the composite film has a certain thickness, it will feel hard. Moreover, TPU film is still in its infancy in China, with low output and unstable quality. It mainly relies on imports and the price is high.
in conclusion
Glitter PU leather has developed rapidly in recent years. During the production process, manufacturers should perform different processing according to different uses and requirements to improve product quality to meet customer requirements to the greatest extent.






Product Overview
Product Name | Glitter synthetic leather |
Material | PVC / 100%PU / 100%polyester / Fabric / Suede / Microfiber / Suede Leather |
Usage | Home Textile, Decorative, Chair, Bag, Furniture, Sofa, Notebook, Gloves, Car Seat, Car, Shoes, Bedding, Mattress, Upholstery, Luggage, Bags,Purses & Totes, Bridal/Special Occasion, Home Decor |
Test ltem | REACH,6P,7P,EN-71,ROHS,DMF,DMFA |
Color | Customized Color |
Type | Artifical Leather |
MOQ | 300 Meters |
Feature | Waterproof, Elastic, Abrasion-Resistant, Metallic, stain Resistant, Stretch, Water Resistant, QUICK-DRY, Wrinkle Resistant, wind proof |
Place of Origin | Guangdong, China |
Backing Technics | nonwoven |
Pattern | Customized Patterns |
Width | 1.35m |
Thickness | 0.6mm-1.4mm |
Brand Name | QS |
Sample | Free sample |
Payment Terms | T/T,T/C,PAYPAL,WEST UNION,MONEY GRAM |
Backing | All kinds of backing can be customized |
Port | Guangzhou/shenzhen Port |
Delivery Time | 15 to 20 days after deposit |
Advantage | High Quanlity |
Glitter Fabric Application
● Apparel: Add sparkle to your wardrobe by using glitter fabric for clothing items such as skirts, dresses, tops, and jackets. You can make a statement with a full glitter garment or use it as an accent to enhance your outfit.
● Accessories: Create eye-catching accessories like bags, clutches, headbands, or bow ties with glitter fabric. These sparkly additions can amp up your look and add a dash of glamour to any ensemble.
● Costumes: Glitter fabric is commonly used in costume-making to add that extra wow factor. Whether you're creating a fairy, princess, superhero, or any other character, the glitter fabric will give your costume a magical touch.
● Home decor: Bring sparkle to your living space with glitter fabric. You can use it to make throw pillows, curtains, table runners, or even wall art to add a touch of glamour to your home.
● Crafts and DIY projects: Get creative with glitter fabric by incorporating it into various craft projects, such as scrapbooking, card-making, or DIY ornaments. The glitter fabric will add shine and depth to your creations.






Our Certificate

Our Service
1. Payment Term:
Usually T/T in advance, Weaterm Union or Moneygram is also acceptable,It's changeable according to client's need.
2. Custom Product:
Welcome to custom Logo & design if have custom drawing document or sample.
Please kindly advice your custom needed, let us desigh high quality products for you.
3. Custom Packing:
We provide a wide range of packing options to suit your needs insert card ,PP film, OPP film, shrinking film, Poly bag with zipper,carton, pallet, etc.
4: Delivery Time:
Usually 20-30 days after order confirmed.
Urgent order can be finished 10-15 days.
5. MOQ:
Negotiable for existing design, try our best to promote good long-term cooperation.
Product Packaging








The materials are usually packed as rolls! There are 40-60 yards one roll, the quantity depends on the thickness and weights of the materials. The standard is easy to move by manpower.
We'll use clear plastic bag for the inside
packing. For the outside packing, we'll use the abrasion resistance plastic woven bag for the outside packing.
Shipping Mark will be made according to the customer request, and cemented on the two ends of the material rolls in order to see it clearly.
Contact us
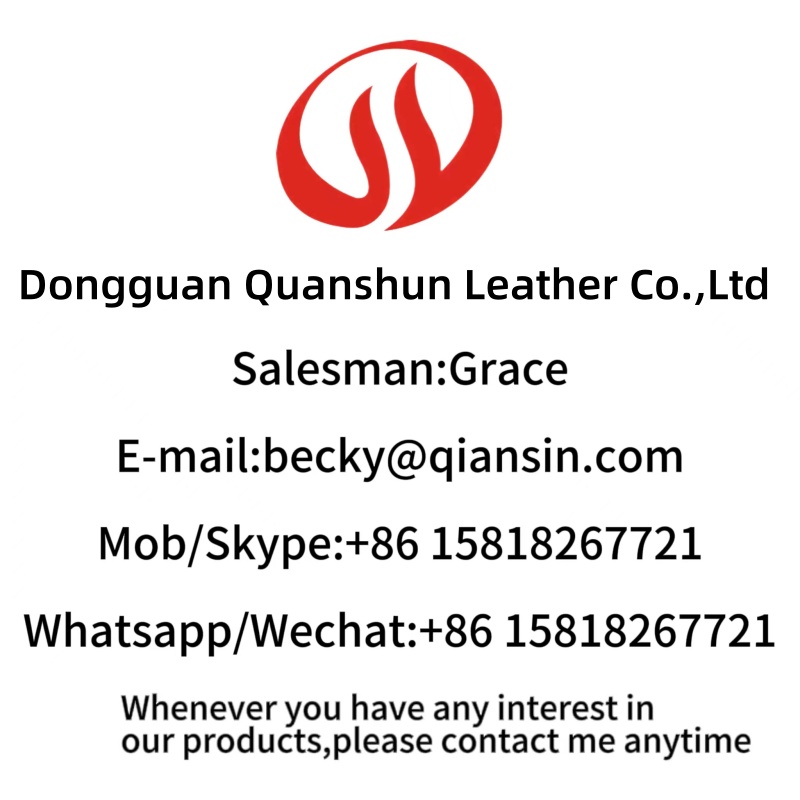